The development of Variable Frequency Drives (VFDs) began as a means to provide basic speed control for AC motors. Over time, technological advancements have made modern VFDs more compact, cost-effective, and user-friendly. These devices allow for precise adjustments to motor speed and torque to meet specific system requirements, resulting in enhanced operational efficiency and energy savings.
However, VFDs also introduce challenges, particularly the generation of motor shaft voltages. When shaft voltages exceed critical thresholds, Electrical Discharge Machining (EDM) occurs, leading to micro-arcing on the bearing surfaces. This phenomenon causes pitting and fluting on bearings, significantly reducing motor lifespan. Implementing effective shaft grounding solutions is essential to mitigate these issues, improve motor performance, and reduce downtime.
Aaki Corp.’s Motor Shaft Grounding Module (MSGM) provides a versatile and reliable solution for managing shaft voltages. Compatible with various motor configurations, it is ideal for a wide range of industrial applications, such as HVAC systems. By preventing EDM damage, the MSGM extends motor component lifespans, enhances system reliability, and reduces costs.
This article explores the fundamentals of VFD driven motors and highlights the importance of shaft grounding to help you make informed decisions for your applications.
What is a Variable Frequency Drive (VFD)?
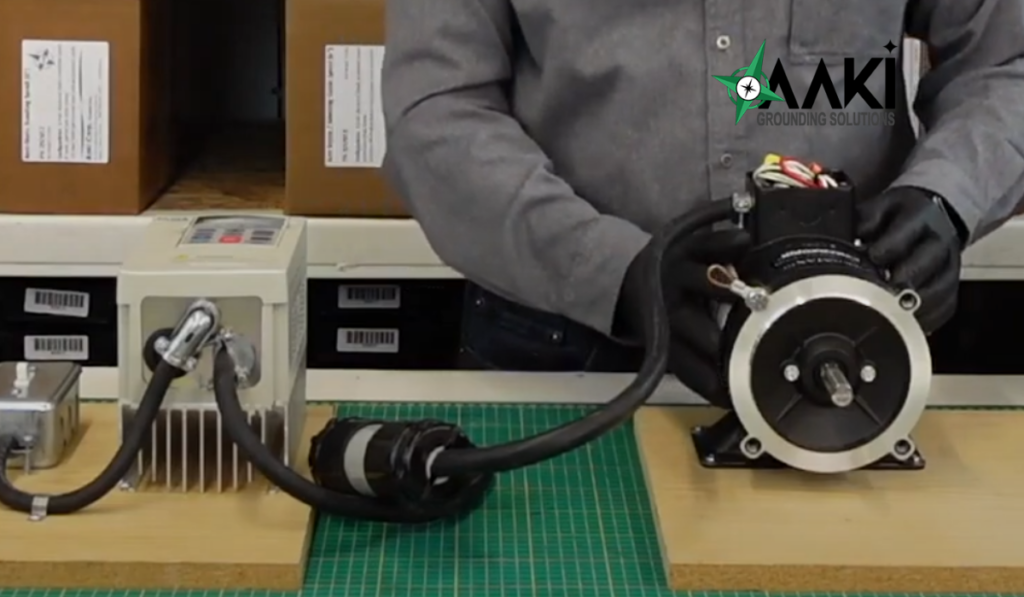
A Variable Frequency Drive (VFD) is an electronic device that controls the speed and torque of an induction motor by varying the frequency and voltage of the supplied power.
- Key Advantages of VFDs:
- Speed Control: Precisely adjust motor speed by modifying the power supply frequency.
- Torque Regulation: Regulate torque across varying speeds for optimal performance.
- Soft Start/Stop: Gradual voltage application reduces mechanical stress, extending equipment life.
- Energy Efficiency: Match motor speed to load requirements, lowering energy consumption.
- Reduced Starting Current: Minimize inrush current during motor startup, reducing peak load requirements.
- Challenges Associated with VFDs
VFDs offer significant benefits, but they also introduce issues that can compromise system reliability:
- Bearing Currents: Shaft voltages induce currents through motor bearings, causing damage.
- Voltage Spikes: High-frequency switching generates voltage spikes that can degrade motor insulation.
- Harmonic Distortion: Introduced harmonic currents lead to overheating and equipment malfunction.
- Electromagnetic Interference (EMI): EMI from VFDs can disrupt nearby electronic devices.
- Applications of VFDs
- HVAC Systems:
- Energy Savings: Adjust motor speed based on demand, reducing energy usage.
- Improved Efficiency: Ensure optimal system performance across operating conditions.
- Reduced Wear: Gradual speed changes minimize mechanical and electrical stress.
- Demand-Based Operation: Dynamically respond to varying load conditions.
- Pumping Systems: Enhance performance and energy efficiency while improving reliability.
- Conveyor Systems: Enable precise control, reduce energy consumption, and lower maintenance costs.
- Machining Centers: Enhance precision and productivity while reducing operational wear and energy usage.
- Saw Mills: Improve cutting efficiency, energy savings, and motor performance under varying load conditions.
- Compressors: Improve energy savings, flexibility, and overall performance.
- Drilling Equipment: Increase operational efficiency and reliability.
- Crusher Mills: Optimize performance and energy efficiency while enhancing process control.
What Causes Bearing Damage in VFDs?
Bearing damage in VFD-controlled motors is primarily caused by shaft voltages and the currents they generate:
- Motor Bearings Insulate the shaft: Although not intuitively obvious, the shaft of a motor is actually electrically isolated from the motor body by the bearings. Bearings ride on a thin layer of grease that is an electrical insulator. In direct three phase line operated induction motors, the differential voltage between the motor shaft and the motor body is very small and does not pose an issue to the bearings.
- VFDs create Voltage Spikes: When VFDs operate, they create high frequency, very short duration electrical pulses that attempt to mimic the overall shape of a sine wave. However, these high frequency pulses capacitively couple energy into the motor shaft. The voltage in the shaft rises, with nowhere to go.
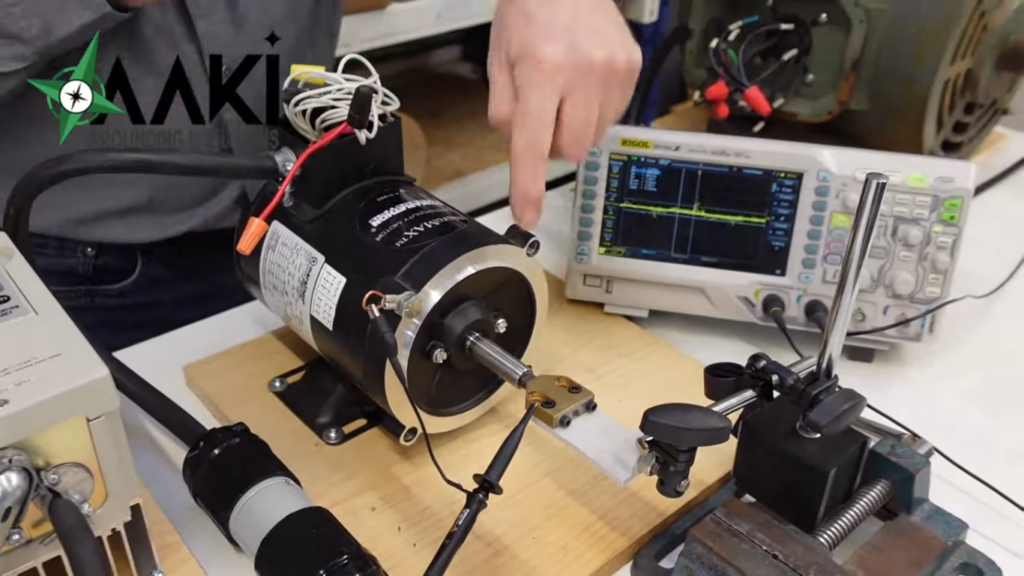
- Electric Discharge Machining: A process known in the machining industry as Electric Discharge Machining or EDM occurs when voltages build up on the motor shaft to a level that exceeds the insulating properties of the grease used in the shaft bearings, discharging through the motor bearings as electrical arcs. These arcs generate intense heat, vaporizing metal on the ball and race of the bearing, forming small craters on the surfaces. Over time, these effects result in pitting and fluting, degrading the bearings’ functionality and leading to premature mechanical failure.
- Grease Degradation: The intense heat generated by EDM damages the lubrication within the bearings. This degradation reduces the grease’s effectiveness, increases friction, and accelerates wear, further contributing to bearing failure.
The Role of Shaft Grounding Devices
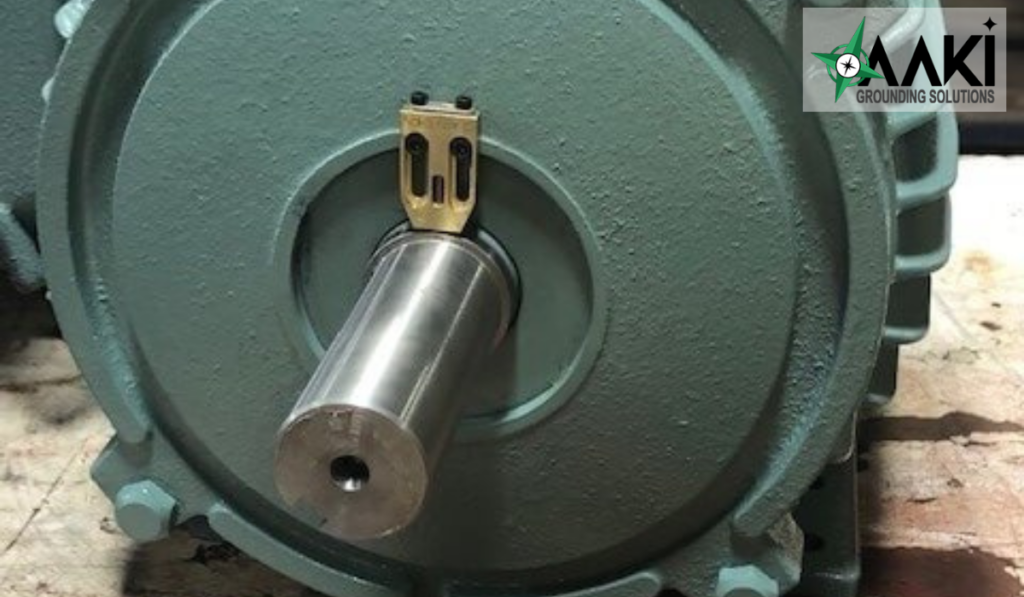
Aaki Motor Shaft Grounding Modules are specifically designed to route shaft voltages directly to the motor body, effectively bypassing the bearings. These devices are critical for enhancing the reliability, and longevity of motors, especially in systems controlled by VFDs.
Aaki’s Motor Shaft Grounding Module (MSGM)
Aaki’s MSGM effectively redirects shaft voltages away from bearings, protecting motors and associated equipment from VFD-induced damage. Key features include:
- High Quality Construction: The housing is manufactured from a single block of aluminum bronze, providing a solid, corrosion-resistant housing built for durability and long-term performance in harsh environments.
- High Copper Content Brush: The grounding brush features high copper content, providing superior conductivity and efficient dissipation of stray currents. The pre – contoured brush is also effective at polishing the motor shaft and filling in small pores with copper, limiting brush wear and increasing operational life.
- Professional Installation: FleXmount™ brackets and the FleXform™ tool ensure precise, quick installation with minimal tools.
- Reduced Installation Time: Aaki’s FleXmount™ brackets significantly reduce installation time and associated manpower costs. The pre-contoured brush can eliminate timely seating procedures.
- Innovative Brush Life Window™ Technology: Real-time visual assessment of brush wear allows the operator to see brush life at a glance eliminating disassembly for inspections, saving time.
- Cost-Effective Performance: Prevents expensive repairs and reduces maintenance costs.
- Low Maintenance: Designed for longevity, typically outlasting the motor’s bearings.
Addressing Challenges in Electric Motor Repair Shops
Electric motor repair shops face significant challenges around labour. These challenges include:
- Labor Shortages: The lack of skilled technicians results in longer installation times and reduced capacity to handle complex tasks.
- Increased Labor Costs: High demand for specialized skills drives up labor expenses, impacting profitability.
- Risk of Installation Errors: Unskilled or less experienced workers make mistakes during installations, leading to improper grounding and potential motor damage, that ultimately impact the installer.
Aaki’s Solutions for Motor Repair Shops
Aaki listens. We take your issues seriously. Through discussion and thoughtful design, Aaki directly addresses these challenges with innovative features created to simplify processes and offer true value:
- Cost-Effective: MSGMs, spacers, brackets and tools are cost effective and priced to offer good value.
- Easy to Install: FleXmount™ brackets and the FleXform™ tool enable technicians to install the module quickly and accurately, minimizing installation time and labor requirements. Typical installations take less than 20 minutes.
- Consistent Installation Process: Standardized design ensures a uniform installation experience across all motor styles, reducing variability and the likelihood of errors.
- Superior Bearing Protection: Aaki MSGMs significantly lower the risk of bearing damage, ensuring longer motor life and reliability.
- Reduced Downtime: Fast and accurate installations minimize motor downtime, reducing service time for repair shops.
- Educational Support: Aaki provides detailed resources, including videos and guides, to train technicians on the benefits and installation of MSGMs. These materials empower repair shops to communicate the value of shaft grounding solutions effectively to clients.
In short, Aaki’s solutions allow motor repair shops to operate more efficiently, reduce costs, and deliver better service for their customers.
Conclusion
Variable Frequency Drives provide precise motor control, improving efficiency and reducing operational costs. However, they introduce challenges like shaft voltages, which can damage bearings and reduce motor lifespan.
Aaki’s Motor Shaft Grounding Module (MSGM) offers a robust solution by preventing shaft voltage-related damage, ensuring reliable motor operation, and reducing maintenance requirements. With features like simplified installation and Brush Life Window™ Technology, Aaki MSGMs are an ideal choice for safeguarding motors in demanding industrial environments.
Contact Aaki today to learn more about how MSGMs can protect your motors and optimize your operations.